Integrated Hospital Logistics with FH
15/04/2025
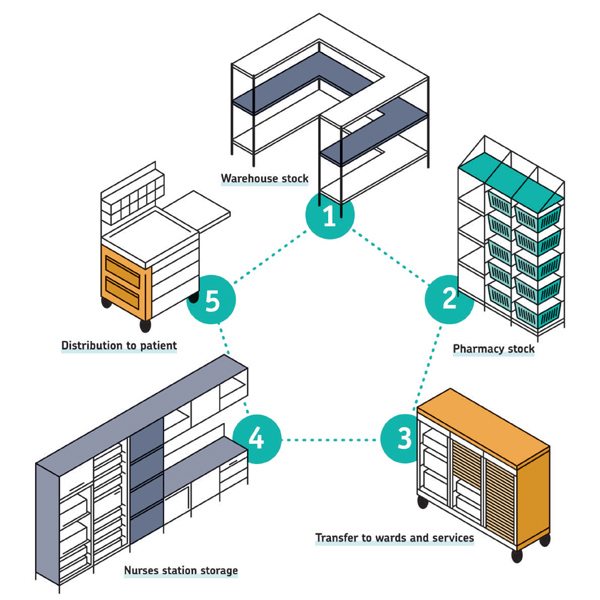
The Current Situation
Hospital logistics face numerous challenges. The arrival of goods (medications, hospital supplies, and various materials) typically occurs in a central area, where storage methods can vary widely. Often, boxes and packaging are temporarily placed on the floor or shelves before being opened and sorted. From there, materials take different paths: they may be stored in trays, distributed among departments, or transported using various tools such as logistic columns, roll containers, and service carts.
Even within departments, inventory management is just as varied, with different storage areas and operational methods that change from one department to another. While this flexibility allows each unit to organize itself according to its specific needs, it also leads to inefficiencies: stock levels are not always monitored, orders are placed based on intuition, materials expire unused, and in some cases, misappropriation occurs.
The Solution: An Integrated Logistics System
To achieve efficient hospital logistics, it is essential to integrate physical and digital management. This means combining advanced software with a well-designed storage and handling system that ensures order, accessibility, and waste reduction. The two fundamental pillars are:
- A computerized system that starts from the patient’s medical record and extends to order management, from the hospital pharmacy to suppliers.
- Harmonization of logistical tools, ensuring compatibility between all components of the supply chain.
A truly integrated logistics system ensures that shelves, trays, and containers are compatible with internal transport means, which in turn fit seamlessly with department storage units such as cabinets and logistic columns. This integration extends all the way to the final point of use (patient bedside, outpatient clinics, operating rooms, etc.).
The Advantages of an Integrated System
The harmonization and standardization of storage containers in hospitals bring numerous benefits. With a single modular system, materials can be easily transferred between shelves, carts, and cabinets without requiring manual reorganization, providing a competitive advantage and improving logistical efficiency.
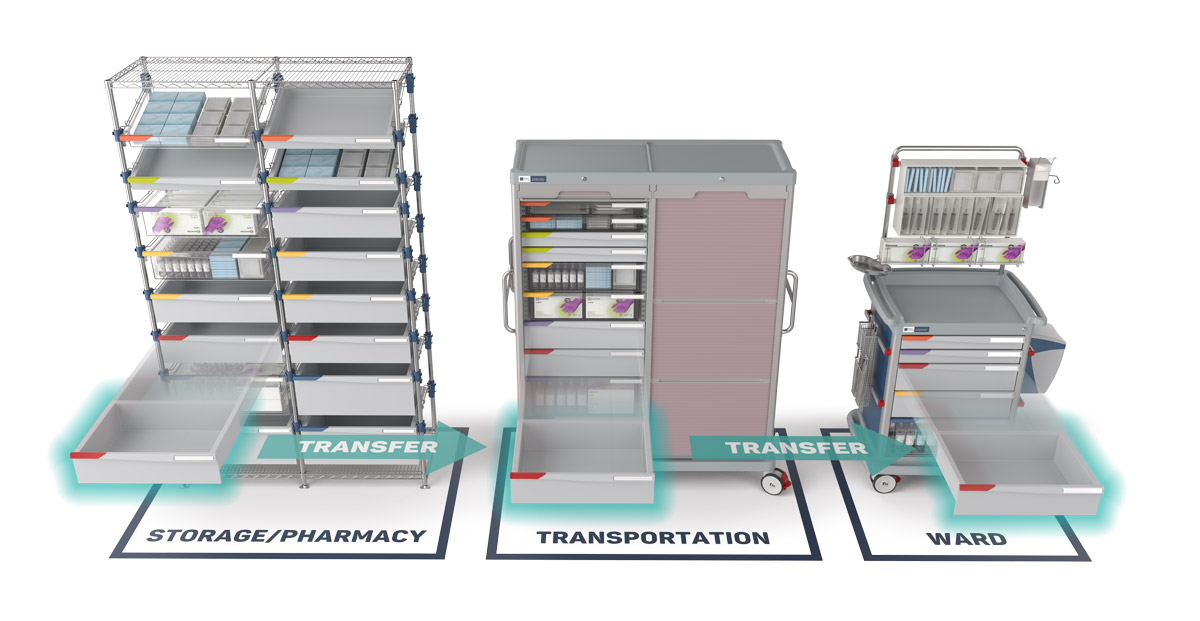
FH’s Solution: EXPER-mod
The key element of FH’s solution is the adoption of EXPER-mod, a system of standard trays/containers (available in widths of 410 mm and 610 mm and in three different heights), already used in PRESTO, PRECISO and TRS columns, and perfectly compatible with MOSYS-ISO.
EXPER-mod is designed for easy transportation and transfer between different logistical units and can be equipped with:
- QR codes and RFID labels, enabling automated tracking;
- Traffic light indicators (red-green) to simplify stock management.
EXPER-mod also supports various inventory management methodologies, such as FIFO (First-In, First-Out), Kanban, and control systems using RFID gates or QR code scanning.
Costs and ROI: An Investment That Pays Off in Record Time
Whatever methodology is used, inefficiencies and waste are a common problem in many hospital pharmacies and hospital warehouses, worldwide.
FH experts are available for an analysis of the situation and a proposed solution to optimize the medication cycle and material flows to reduce waste and inefficiencies. investment in an integrated logistics solution guarantees a quick and tangible ROI.
Thanks to FH’s solution, hospital logistics become more efficient, reducing waste, improving traceability, and optimizing resources. A small change that makes a big difference!
Contact us or reach out for a chat with an expert in the field.